Introduction
The rising cost of energy has put strain on many sectors across the UK and other parts of the world, as we are facing an unprecedented rise in wholesale gas and electricity prices.
Since January 2021, wholesale gas prices have risen by 250%.
Sectors are now facing uncertain import supply, which is negatively affecting the manufacturing production and processes.
While we cannot control the current market, we can provide you with tips on how to reduce your upcoming costs throughout your business this winter.
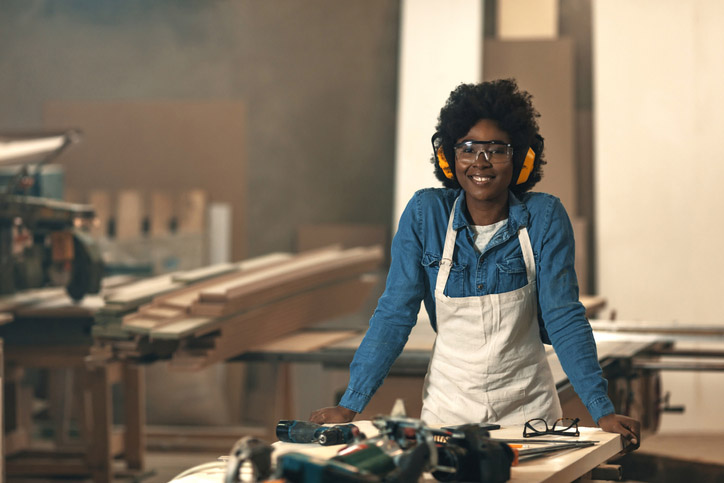
What this means for the manufacturing, warehouse and logistics industry
Companies are under intense pressure to cut costs across manufacturing, warehousing and logistics.
These industries are major users of natural gas and electricity.
The energy intensive industries including chemicals, steel and paper are now suffering a significant increase in their costs.
The current spike in energy costs has threatened to shut down, production leading to increasing concerns about the industry.
Energy efficiency is one of the simplest ways to achieve such savings.
Most businesses are already committed to challenging energy efficiency targets. They understand the reputational benefits of reducing their carbon footprint and demonstrating corporate social responsibility to stakeholders.
Furthermore, according to a recent CBI report, energy prices for medium-sized users are predicted to grow by almost 30 percent in the next five years. So, if companies fail to cut energy consumption soon, they are going to be left even more out of pocket.
Where is the most energy wasted?
According to the Carbon Trust, industry is responsible for 17 percent of the UK’s total energy use—and most of that results from manufacturing. The same figures show that 11 percent of all energy consumed by manufacturing is used for space heating, rising to 45 percent in some subsectors.
However, in the warehousing and logistics industry, it is lighting that uses most of the energy (typically around 65 percent). Energy efficiency in this sector is particularly important because it is growing so quickly. Warehousing capacity in the UK has almost doubled in the past decade, driven by the rise of online retail.
Where are the opportunities for energy saving?
Business heating, ventilating, and lighting may feel like fixed costs, but a saving of approximately 20 percent on each is achievable in many circumstances. It’s also possible to make similar savings on industrial processes and running machinery.
Let’s look at them one at a time:
What has happened to the current energy market
Heating
Typical manufacturing and warehousing premises are big open spaces. They have high ceilings, delivery doors that are often left open, and lots of ventilation. All of these can easily lead to heat loss and wasted energy. The Carbon Trust states that many companies in the manufacturing sector could save 20 percent on their heating bills (up to 4 percent of their total energy expenditure) by implementing necessary changes.
Avoid overheating
The temperatures you should be aiming to maintain vary greatly across different types of workplace, even within the same building. However, the principle of avoiding overheating applies everywhere. Heating costs for a business rise by around eight percent for every extra degree Celsius of overheating. As a guide to setting thermostats, the recommended internal temperatures for different types of space are:
- Office 19-21°C
- Workshop 16-21°C
- Heavy work 11-14°C
- Stores 15°C
- Warehousing 16°C, or 13°C when work involves a lot of physical activity.
Switch from convective to radiant heating
Blown warm air, such as that produced by fan heaters, soon dissipates in high-ceilinged buildings. Instead, use radiant warmth from radiators and space heaters. This is more cost-effective in such spaces because it heats workstations directly, focusing the warmth where it is needed.
Check steam boilers
A poorly maintained boiler can consume 10 percent more energy than necessary. Conversely, efficient steam generation and distribution can reduce energy costs by 10 to 30 percent.
Experts recommend regular boiler checks and an annual service. Both will ensure that heat exchangers are cleaned, combustion/flue gas is tested, and the fuel is adjusted for efficiency.
A steam boiler can lose up to 10 percent of its heat through insufficient insulation of the distribution system. Look out for wisps of escaping steam from pipes, flanges and joints — a sure sign of a leak. A single 3mm hole in a steam system could cost your business around £1,700 per year.
More ways to save heating costs
- Check your thermostats. In many instances, thermostats are altered temporarily because of weather or work schedules, then forgotten about, so the wrong setting becomes permanent. Companies have saved 10 percent on heating by checking their thermostats regularly.
- Check if employees open windows regularly during the winter months — it’s a clear sign that thermostats are too high.
- Check timers regularly. Make sure you are not heating empty space.
- Avoid heating corridors, stairwells and storage rooms
- Move thermostats away from heat sources, draughts and direct sunlight, so they reflect the real temperature
Ventilation and air conditioning
Ventilation is essential to many manufacturing processes. Therefore, it’s easy to leave alone if there are no apparent problems, but this may perpetuate inefficiency.
Regular system reviews are essential, and you should always turn ventilation off when not required. Using it unnecessarily can be doubly wasteful, because incoming air needs to be heated. Thus, it is wise to check that extractors are not left on outside working hours.
Ventilation tips:
- Consider automating ventilation controls with timers, occupancy sensors or controls linked to machinery.
- Localise ventilation to reduce costs. Some manufacturing processes need ventilation, but it is important to separate them in self-contained areas. This will prevent the ventilation from being overworked because it is drawing in air from beyond the immediate area.
- Fit back draught shutters or dampers to prevent air from blowing through fans when they are not in use. Also, keep them clean.
Ventilation in warehousing
Many warehouses rely on natural ventilation from windows, doors and roof vents. If artificial ventilation is required, consider adding destratification fans to the system. They redistribute rising hot air back to floor level where people are, reducing the need for extra heating.
Air conditioning
Air conditioning is defined as a system that controls temperature, humidity and air quality. A system that just cools the space in hot weather, however, is more accurately described as comfort cooling.
The big question to ask about real air conditioning is “do we need it?” It’s a question that’s worth considering carefully, as an air-conditioned building uses approximately twice the energy of a naturally ventilated building.
New developments can often replace expensive air conditioning. They can include natural and passive ventilation, mixed-mode operation and low energy cooling systems.
Control temperatures and times
As with heating, air conditioning controls are often altered in response to temporary conditions, then never reset. Check for this regularly. Also, make sure that the trigger temperature for AC is not too low. Many guides recommend that air conditioning should not activate until the temperature reaches 24°C.
Make sure there’s a dead band between the trigger temperatures for heating and air conditioning systems. Without a difference of at least 4°C, the heating and cooling can end up fighting each other, wasting energy in the process.
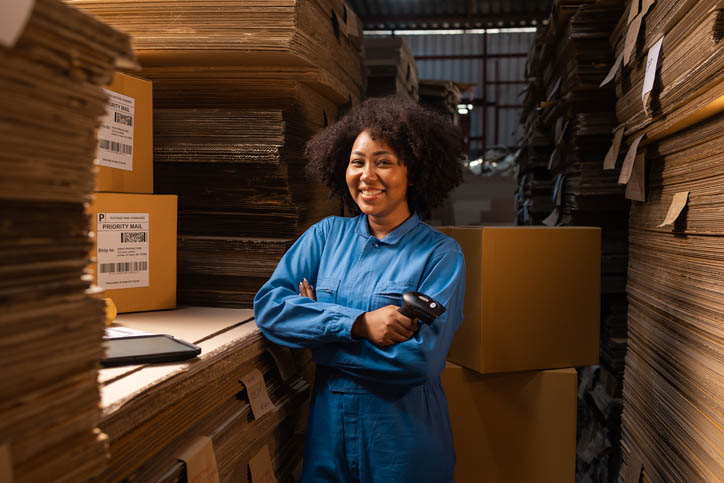
Lighting
Lighting is typically responsible for 10 percent of all energy costs in industrial businesses, and 65 to 95 percent in warehouses. As such, here are a few tips for making significant savings.
Switch off
Often lighting in big industrial units or warehouses is left on all day for shift work. Turning lights off when not in use can lead to a 10 percent saving on overall energy costs.
- Use posters and stickers to encourage a culture of turning lights off when not in use.
- Label light switches, so people know how to switch them on and off.
- Check if lights are left on when everyone has gone. Your cleaning and security staff will know.
Keep windows, skylights and light fittings clean
The Carbon Trust has shown that, in certain premises, natural light levels fall by 30 percent over two to three years due to dust and grime. Such simple maintenance has been shown to reduce business energy costs by around 15 percent. Not only will regular cleaning save money, but it will also make your business look smarter.
Switch to low energy lighting
Light-emitting diodes (LED) have the highest efficiency and life of all widely used bulbs. Switching to LEDs could save up to 80 percent of what you are currently paying to run traditional tungsten bulbs and fluorescent tubes. There are further advantages too:
- Less bulb changing lowers maintenance costs
- You will experience brighter, better quality light
- There is less heat emitted, so cooling bills are lower
- LEDs tend to be dimmable, and therefore more controllable.
Take control
Even the most efficient lights waste energy when not turned off. Automated controls, timers, and movement sensors all help to minimise light waste by turning them off when not in use. A mix can reduce lighting costs by 30-50 percent in all types of industrial building and warehousing.
The building fabric
It is common for industrial buildings to become tired after years of use. Typically, little attention is paid to walls, doors, windows and roofs until a leak, a hole or some other major problem occurs. Yet maintaining the building fabric is a simple and effective way to minimise heat loss, while also protecting the value of the property.
Keeping the building in good repair means regularly checking for roof leaks and blocked gutters or damaged windows. This practice is an essential part of reducing energy bills, and will help to prevent draughts or damp conditions that cause people to turn the heating up.
Higher morale and productivity
People respond positively to comfortable and attractive working environments. Reducing draughts and other problems can help to improve staff morale and enhance productivity, as well as keep energy consumption down.
Other building improvements that can enhance energy performance are:
- Separating warm and cold spaces
- Fitting doors with airlocks or draught lobbies
- Fitting PVC curtains to keep specific areas warm
- Fitting high-speed roller doors to minimise the time loading doors are open
Insulation
At least 25 percent of a building’s heat can escape through an uninsulated single skin roof. Also, insulating cavity walls can reduce heat loss by up to 50 percent. Therefore, you should insulate all pipes, valves and flanges—and keep them in good condition. Also minimise heat escape through windows, skylights, lofts and cavity walls. Try polycarbonate secondary glazing to insulate skylights.
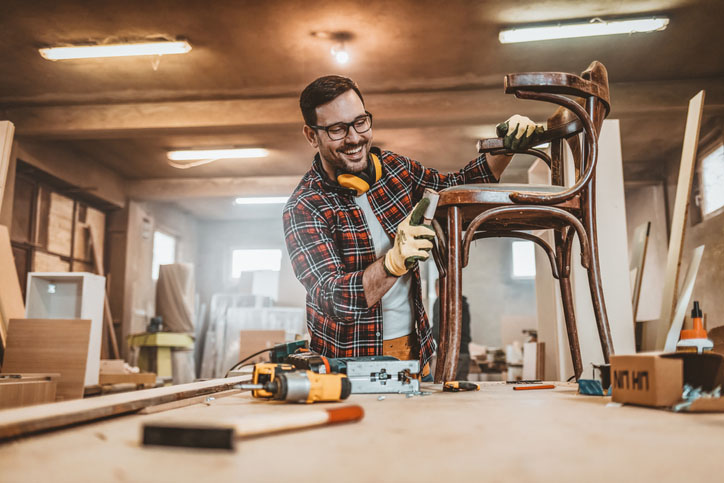
Industrial equipment
Only use compressed air when necessary
Some businesses misuse compressed air for tasks such as drying components and cleaning machinery. Low-pressure blowers and vacuums are far more efficient and effective for these purposes. Use signs and educate your workforce about when and when not to use compressed air.
Look out for leaks
Compressed air equipment found on many industrial sites shows leakage rates of up 30 percent. A simple way to detect leaks is by running a soapy solution through the system and checking for bubbles.
Use cold air to save energy
Using cold air from outside is a simple way to make compressors more efficient. The air is denser and therefore requires less compression. For every 4°C drop in the temperature of the air taken in, energy efficiency improves by 1 percent.
Motors and drives
Motors use an estimated quarter of all electrical energy on manufacturing sites. It should come as no surprise, as a fully-loaded motor typically consumes its purchase cost in electricity in 30-40 days of continuous running. Start making savings by switching motors off when not in use and ignore the myth that it is more efficient to leave it running. Other tips for motor efficiency include:
- Keep motors well-maintained to reduce their energy consumption by up to 7 percent.
- Use predictive software, which tells you when a part needs replacing.
- Check that the motor isn’t too big (many motors are around 20 percent over-sized).
- Changing the connection mode can result in five to ten percent savings, so speak to your motor supplier.
- Modern motors are five percent more energy-efficient, so it may be more cost-effective to replace an old motor rather than rewind it.
- Use a variable speed drive (VSD). Reducing your motor’s speed by 20 percent can cut energy consumption by around 50 percent.
Process heating
Dryers, ovens and heated tanks can be made more efficient by:
- Operating them less frequently and ensuring that there is a full load each time
- Recovering waste heat by using it for space or water heating, or for pre-heating products.
Dryers can use up to 30 percent of the total energy consumed in the food and drink industries, so keep them well-maintained. Check for damaged insulation, clogged air filters and air leaks. Above all, make sure products are not being over-dried.
Ovens
There are two types of oven typically used in manufacturing—batch and continuous. Ovens are used for everything from baking foods to curing paint. Tips for increasing oven efficiency include:
- Inspect and maintain the equipment for broken seals, damaged insulation and air leaks.
- Use automatic process control to minimise heat-up time.
- Don’t leave doors open any longer than necessary.
- Retain heat by fitting air curtains to continuous ovens. Staff should be able to stand nearby comfortably if curtains are working correctly.
Hot liquid tanks
Tanks are widely used for processes like glazing, degreasing and metal treatment. The key to efficiency is to reduce evaporation loss. Measures such as fitting lids and regulating solution agitation have proven to lower heat loss by 50 percent. And insulating tanks with 50mm insulation can save 90 percent of heat energy.
Process cooling
Three main types of process cooling are used across manufacturing industry: air cooling, water-cooling and refrigeration. Promote efficiency by:
- Measuring and monitoring energy use with sub-meters. You should see a direct relationship between demand for electricity and production output. If demand is going up, but productivity isn’t, that means the cooling system is not under effective control
- Set target temperatures and check for overcooling.
Forklifts, cranes and automated warehousing
Forklifts typically consume seven to ten percent of a warehousing or logistics company’s on-premises energy. Simple ways to reduce the energy consumption of product moving equipment include:
- Charging electric forklifts overnight when tariffs are lower.
- Considering automated warehousing solutions. They can minimise the space required for storage, meaning less lighting and heating is needed in the building.
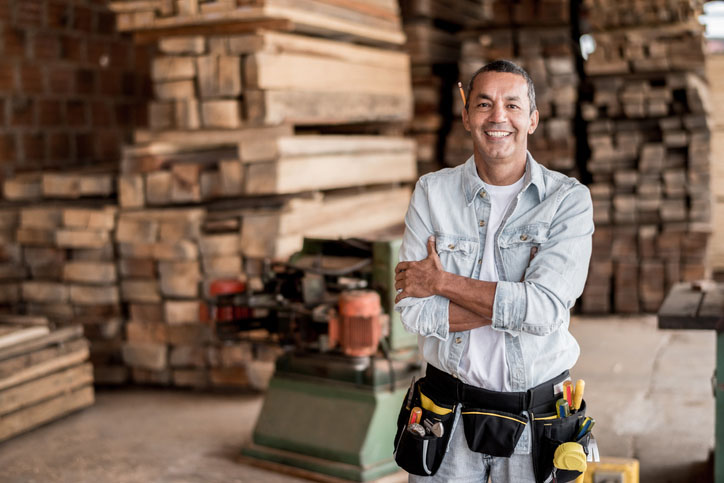
Ready to save energy? Here’s where to start
Now you know to make significant energy savings in your business. Here is how to start today:
- Conduct an inspection and use it to create a checklist of the energy-saving measures you need to implement
- Develop an energy efficiency policy and give it to everyone in the business.
- Allocate clear roles and prioritise actions.
- Regularly monitor your energy consumption, so when there’s an improvement, you know about it.
- Create a graph of energy use against production levels so that you can determine the relationship.
- Set realistic targets and deadlines for improvements—don’t let problems drift. A five percent improvement per year is good.
We encourage all of our customers to do what they can in making the smartest decision for their business energy. Give our friendly team a call and we’ll help you through your best options.